Checklist: Steps to Create and Validate a 3DCS Tolerance Analysis Model
Creating accurate models can be difficult. There are a variety of steps and tools that need to be used in order to get results that can be applied to manufacturing with confidence.
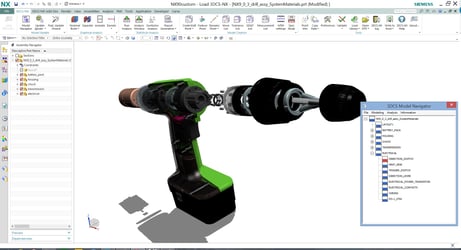
Modeling and simulation are important to reducing costs, but can be intimidating prospects for new users.
3DCS, by its very nature of being an advanced tolerance analysis tool, can be complicated for new users. Many of these users are at a loss when it comes to starting a new model on their own. Here is a checklist to help you with your modeling process.
For more details on individual steps and processes, visit and register at the DCS Community: https://community.3dcs.com

- Modifying the Assembly (Preparing):
- Clearly identify the number, location, nominal and assembly specifications of the Build Objectives or measurements to be analyzed.
- Identify the number of assemblies, components, fixtures, or gages required in the tolerance path to analyze all the desired Objectives.
- Load the appropriate release level assemblies or components into the appropriate NX, 3DEXPERIENCE, CATIA V5 or Multi-CAD solution.
- Create the product assembly tree in accordance to the manufacturing assembly process.
- Create assembly fixtures or gages where required.
- Applying the Assembly Process (Moves):
- Identify the functional features on each component and their relationships to the other components, assembly fixtures or gages.
- Create the appropriate 3DCS move for each component and sub-assembly in accordance to the actual manufacturing process. (Hole-Pin Floats, Manual Adjustments, Deformations or Conditional Assembly logic may require additional moves to be created)
- Visually verify the component and assembly process behavior through the animation function.
- Defining Tolerances (Tolerances GD&T):
- Define part tolerances based on GD&T, actual part capability (CMM Data) or generic tolerances at functional surfaces and measurement locations.
- Visually verify tolerance on the components features or points.
- Build Objectives (Measures)
- Create individual measurements at each toleranced feature or point. Run Simulation to assure toleranced points are within the specified range.
- Create measurements between the target and object points/features for each move. Run Simulation to assure that the object and target features are properly aligned or within the allowable hole to pin float.
- Create the final Build Objectives at the specified locations.
- Visually verify all measurements nominal and Vector Directions
- Results
- Perform Monte Carlo Statistical Analyses. Run Simulation.
- Review the nominal, mean and 6 sigma of each measurement. Utilize other statistical outputs if non-normal distributions are identified.
- Perform HLM Sensitivity Analysis and evaluate tolerance contributions for each measurement. Identify if each contributor is in the datum flow or tolerance loop.
- Perform GeoFactor Analysis to identify geometric factors that may have produced any unexpected Simulation or Sensitivity results.
- Report the Results
- Create a Report that indicates the assumptions utilized in the 3DCS model.
- Create MTM notes and descriptions to describe each for understanding the model and the report.
- Create a Management Report to share the results with managers and colleagues.
Interested in more? Click here to join the free DCS webinar series to learn more about 3DCS Version 7.5 and its new features
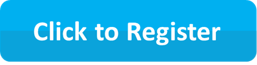
No Comments Yet
Let us know what you think